A manufacturer of tailored tools.
TWT seeks to distinguish itself from much bigger competitors by implementing fast response and individual solutions. “The client receives from us an independent product that differs from any other offering. We don’t just sell tools, we also design the production process for the client”Pellitteri explains.

The engineering department and its five specialists, run by Massimiliano Zuani, plays a key role in this because it is the Production/Client interface. Its task is to find the best tool solution for the specific client, tailored to the window systems to be manufactured and to the machine. In addition to the high quality and to compliance with legal requirements, this must also guarantee that the production is as rational as possible.
Drawings are drafted for each client profile, in which the position in the machine is specified. This activity may require various weeks of work for an extensive project such as Rauh Fensterbau. As an alternative to the drawings, the Software Houses that work with TWT receive the data in text format, a fact that greatly simplifies programming.
The technicians of the software department design the tools taking into account all essential aspects such as maximum weights and dimensions, safety requisites and ease of assembly. With the help of state of the art CAD/CAM systems, the data are prepared for production, while simulations help exclude the likelihood of possible collisions. Finally, autonomous production of the tools conceived at the beginning is made possible.
Solutions for the windows market
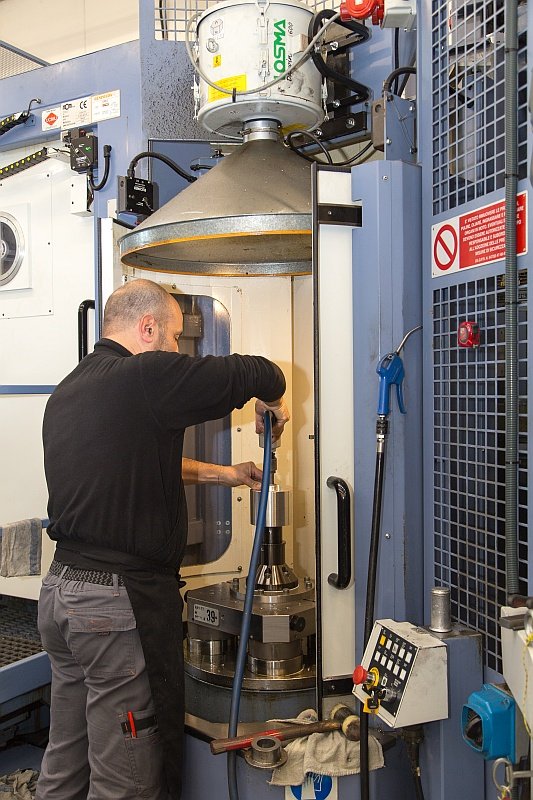
An example of a TWT product that explains the role of system developer is the Esperia Life system for the Italian and Spanish markets. With the construction of a retractable profile, the tool manufacturer meets the demand for windows with narrow lights for renovations.
For the German market especially and in cooperation with the clients, the “Prüller corner joints ”have been developed with a mortise and tenon joint (see interview in inset)as well as the TWT Style projectthat does not require management of the glazing bead during production.
Another item placed on the market is a system of windows that meets the special needs of British clients. “Our sales reps influence our decisions, an aspect that is not possible in large-sized companies” Pellitteri says.
Customer relations also becomes simpler: TWT technicians can always enter in direct contact with the people in charge of Production and Assembly.
Very high quality standards
“A defective tool can mean significant costs for a client and delays delivery. Thanks to rigorous and coherent quality control, we do our best to prevent this from happening. All production employees are responsible for quality assurance in their own work area, as if they were suppliers of the colleagues that are called to execute further work phases next to them”, Cristian Zuani explains.
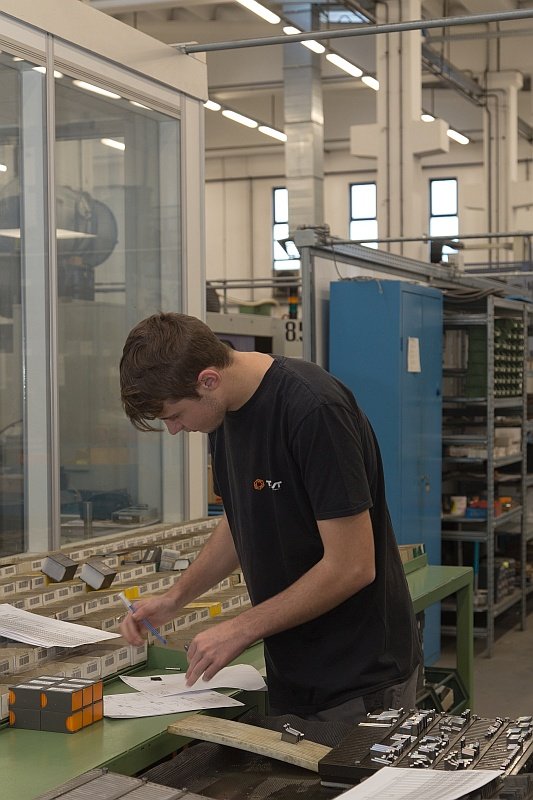
Another way of guaranteeing top quality standards is the exceptionally high level of vertical integration – 90% – so that all work phases significantly linked to quality are kept under direct control.
The washers for the main body of the tools are cut from steel and aluminium pressure bolts. For weight reasons and due to the increasing use of CNC machines, mainly aluminium alloy is used, the same as that used in the aircraft manufacturing sector. All parts can be tracked back to the initial roll of material. With a generously large stock, the company stays independent from offer fluctuations.
A bar code is assigned to each disc, and via this code the drawing of the tool can be uploaded to the display when the client has questions. Moreover, with this code it is possible to always keep track of the piece during production.
For processing, the discs are fastened to large and very heavy base plates so as to ensure vibrations as low as possible and very high dimensional accuracy. Anyhow, processing procedures are simulated in advance.
The company has its own galvanising system for nickel-plating the steel base. In the past, this step was outsourced.
“Today we are significantly quicker with our own surface treatment system. This is a great advantage for the client who has had problems and needs a replacement tool as quickly as possible”, Alberto Zuani says.
Delivered to the client within 24 hours
Spare blades are manufactured in a dedicated department, and usually are delivered within two or three weeks. “In truly urgent cases, we can also produce them more quickly, so that the client receives them within 24 hours ” Rauscher assures us.

During the sharpening process, the blades are rinsed with cooled oil so as to limit the tolerances associated with overheating.
Prior to dispatch, the tools are sample-checked under the microscope to verify their compliance with the dimension standards and for defects on the surface or in the fissures of the connection area.The microscope is used also to acquire models and create drawings for post-production.
The system currently has from 250,000 to300,000blade geometries on file.
TWT also guarantees that the blades can be re-ordered in the same quantity of raw material even after 30 years. All tools are balanced after assembly. The report is given to the client, and a wood sample is supplied together with the tool for better comprehension. A QR code on the tool simplifies its identification and provides all of the information necessary, such as that required to order spare parts.
Doubling of the tool’s useful life
TWT has been offering its clients interchangeable inserts with a nano-structured coating since2011. The NaDia Diamond coating extends useful life by up to 300%. The longer life of the cutters shortens preparation time while increasing productivity and at the same reducing unit costs.
TWT has developed the special coating together with the Faculty of Physics of the University of Trento and with the Fondazione Bruno Kessler foundation. The perfecting of the procedure took two years. The coating is applied in-house using the PE-CVD (Plasma Enhanced Chemical Vapour Deposition) process.
The sp2 (graphite) and sp3 (diamond) low-temperature hybridised carbon layers arebonded together. The diamond content provides the DLC (Diamond-Like Carbon) layer with extremely high hardness properties, while the graphite acts as substrate. This process is performed at low temperatures so as not to change the structure of the Widia blades.
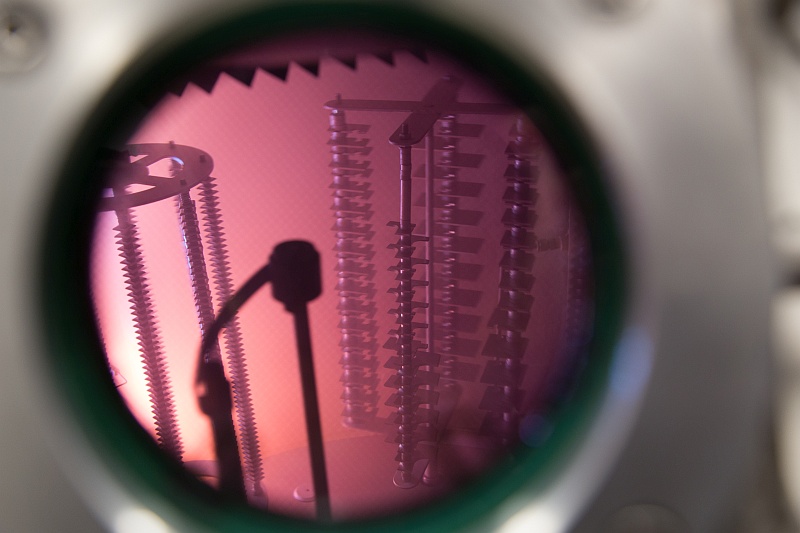
Convincing properties
The result is a coating made up of twelve 1 micron thick layers. The process can be used on all common cutters, independently from their blade profile and thickness.
Its extreme hardness is accompanied by a significantly higher resistance to abrasion, a lower cutting pressure due to the delayed rounding of the cutting edge, and lower resinification of the cutter due to the surface structure.
“The application of the coating results in the rounding of the cutting edge by about one thousandth, but this value is significantly lower than with other technologies” says Martin Rauscher, the CEO of Zuani Deutschland GmbH.
Accurately tested
In connection with the new nano-coating, TWT speaks of duration doubling. In actual fact, clients report periods of duration from 2.5 to 3 times longer. The result was obtained with a wide range of materials (solid wood, glulam and plywood). Today, special tools and cutters are also coated for third parties. The company benefits from the fact that the coating is biocompatible.


